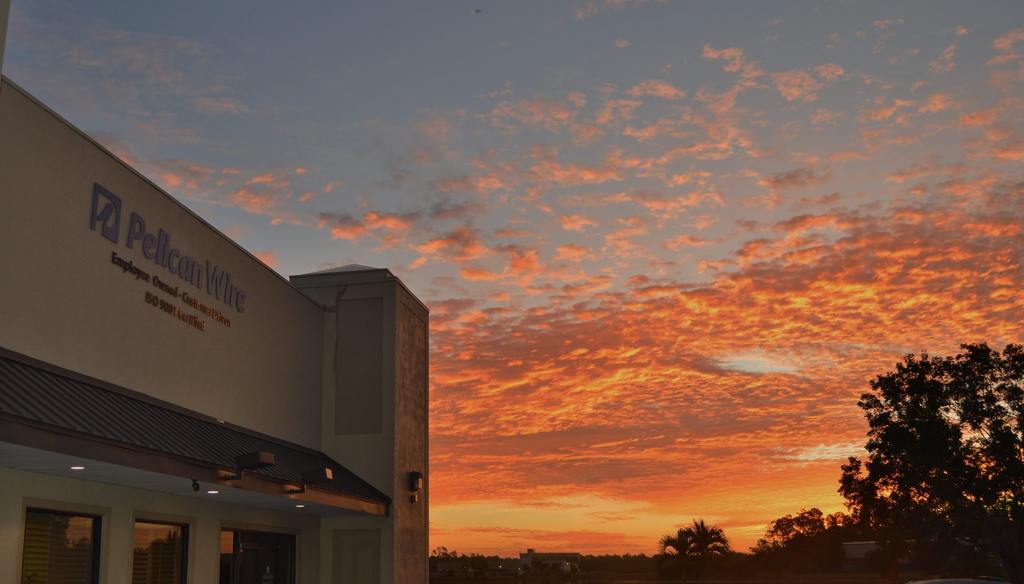
With decades of innovation and hard work in their portfolio of experience, Pelican Wire leads in thermocouple wire manufacturing. Wires attached to thermocouples lie at the heart of measuring temperature in many industrial operations, forming a part of the quest for precision and the need to monitor thermal conditions. We shall further elaborate on the details of the thermocouple wire, types, application, and art in selecting the most appropriate one for varying needs. Stay tuned till the end of the blog.
Types of Thermocouple Wires
The spectrum of thermocouple wires includes many types, each carefully engineered to excel in a particular environment and range of temperatures:
Exploring the Range: K Type, J Type, T Type, and Beyond
- K Type: It is very flexible and can be used generally. This works very efficiently within the temperature range of -200°C to 1260°C.
- J Type: Made up of iron and constantan, this is reliable over a temperature range of -210°C to 760°C and most valuable to the applications of 760°C.
- T Type: This product uses copper and constantan and serves environments ranging from -200°C to 400°C. It can serve applications at low temperatures with very high accuracy and stability.
Beyond these commonly known types, many variations exist, each tailored to address distinct requirements with precision and efficacy.
Specialty Thermocouples: High Temperature, Low Temperature, and Exotic Alloys
In extremely high or low-temperature environments, specialty thermocouple wires become invaluable resources, enabling measurements to be taken where the usual choices would fail:
- High-temperature thermocouples: These are manufactured from solid alloys, ensuring high resiliency for effective furnace monitoring in aerospace applications and demanding industrial processes.
- Low-temperature thermocouples: They navigate conditions well below zero with finesse, ensuring precision in cryogenic experiments and refrigeration systems.
- Exotic Alloy Compositions: Unlocking potential beyond conventional boundaries, creating made-to-measure solutions for the harshest thermal environments.
- Tailored Solutions: Tailor Thermocouple Wires to your unique requirements.
Custom Solutions: Tailoring Thermocouple Wires to Unique Needs
Pelican Wire’s prowess extends beyond standard offerings, empowering clients with bespoke solutions meticulously crafted to address specific challenges:
- Leveraging advanced manufacturing capabilities and expertise, Pelican Wire collaborates closely with clients to conceptualize and realize custom thermocouple wires tailored to their precise requirements.
- Through a series of case studies, we illuminate the transformative impact of these tailored solutions, showcasing instances where Pelican Wire’s ingenuity transcended expectations, revolutionizing temperature monitoring across diverse applications.
Applications and Industries
The flexibility and reliability of the thermocouple wire make this small but important component critical in everything from industrial goods manufacturing to gourmet cooking and space missions. Let’s learn more about how thermocouple wires facilitate excellence in manufacturing, culinary precision, and exploration beyond Earth.
Manufacturing Excellence: Thermocouple Wires for Industrial Use
In the entire process of industries, thermocouple wires are supreme in bringing about accuracy and effectiveness across countless operations. From automotive manufacturing to petrochemical refineries, a thermocouple wire is a sentinel, constantly watchful, monitoring the rise and fall of temperatures to bestir production processes and serve final product quality. In this direction, through real-world examples, we attempt to deconstruct the complex symbiosis between thermocouple wires and industrial efficiency, making their indispensability in driving excellence in the context of manufacturing.
Thermocouple Wires: A Culinary Precision in the Food Industry
Thermocouple wires are the unsung heroes of perfection in a world of exacting culinary standards. They ensure the right temperature, guided by strict guidelines, for these wires to manage the subtleties involved with food and its processing and preparation to keep its flavour and support food safety. These thermocouple wires control temperatures so well that they keep up with industry standards without the possibility of danger from undercooked or overcooked foods while ensuring that the food is at its best, just in terms of flavour and texture.
Beyond the Earth: Aerospace and Exploration-Thermocouple Wires
The boundless frontiers of space exploration demand technologies that are up to the task of withstanding the cosmos’ rigours, and where the thermocouple wires do not give in, the determination is matched. Critical information is yielded from these wires, which are essential in successfully running missions, from spacecraft propulsion systems to planetary rovers moving in the space vacuum and the hostile environment of alien worlds. In the aerospace application alone, we look deep into these complexities and explore innovations that drive thermocouple wire design to assure reliability amidst this unforgiving expanse of space.
Factors Influencing Selection of Thermocouple Wires
Several factors call for careful consideration when selecting the correct thermocouple wires to ensure they perform with the desired reliability. Below are key points to consider
Temperature Range: Wire Type Matching the Application
- It is extremely important to choose thermocouple wires that are calibrated in the expected temperature range at which they will work.
- Appropriate wires for temperature conditions ensure accurate and reliable measurements in extreme heat or sub-zero environments.
Environmental: Corrosion, Vibration, and Pressure
- Environmental factors such as temperature, pressure, and vibration contribute to the corrosion performance of thermocouple wires.
- The choice of wires made to resist corrosion and withstand the effects of environmental stressors ensures a longer operational life and maintains measurement accuracy.
Correctness and Accuracy: Quality Requirements Met
- Precision and accuracy are highly critical requirements in applications for temperature measurement.
- This is why the thermocouple wires are chosen to be reliable and stable; hence, measurements can achieve industry standards, which also means that trust and operational excellence can be introduced.
Cost-Effectiveness: Balancing Performance with Budget Constraints
- As much as performance counts the most, it is equally important to balance performance with the relevant budget constraints.
- Selecting the thermocouple wires with the best performance under such budget constraints would enable the operator to make full use of available resources without compromising quality and reliability.
Compatibility: Ensuring Interoperability with Measuring Instruments
- It should ideally integrate seamlessly with instruments used for measurement.
- Ensure compatibility and comply with industry standards to guarantee deployment without a hitch, minimal disturbance, and optimization of the workflow continuum.
It is apparent that operators can choose the thermocouple wires relevant to their needs based on factors such as temperature range, environmental condition, accuracy, cost, and compatibility.
Best Practices for Installation and Maintenance
The thermocouple wires are vital to any temperature measurement system, and their accuracy and reliability are conditioned by proper installation and regular maintenance. The following section outlines some critical strategies to optimize proper installation and maintenance practices.
Proper Installation Techniques
Before proceeding with the installation, it is imperative to note that the thermocouple wire measurement should be very accurate and correct. The subsequent steps, made following the most advanced industry procedures employing specialized tools and equipment, provide perfect sensor fitment and reduce the chance of any measurement anomalies:
- Detailed Planning: First, conduct a thorough evaluation of the site for installing the equipment, taking into account factors like ambient temperature variation, potential sources of electromagnetic interference, and accessibility for maintenance.
- Proper Positioning of Sensors: Locate the thermocouple sensors at those points in the system most representative of the temperature to be monitored. Consider any influence of heat gradients, airflow, or material composition.
- Proper Termination: Terminate thermocouple wires into instrumentation using appropriate methods, such as welding, crimping, or compression fittings where the cables are snugly attached.
- Shielding and Grounding: The effective use of shielding techniques and proper grounding practices go a long way in minimizing electrical noise and interference that may compromise the accuracy of measurements.
Routine Maintenance:
There are maintenance practices structured for these, which could help in retaining the integrity and longevity of the thermocouple wires:
- Periodic Inspection: From time to time, inspect thermocouple wires for signs of wear, corrosion, or physical damages that can affect performance. Damaged parts must be changed promptly to ensure the correct temperature measurements.
- Calibration Check: Schedule periodic calibration checks to ascertain that the temperature is measured correctly and recalibrate the measuring instrument if needed. This will ensure uniformity and reliability in data acquisition, especially in these critical processes that call for precision.
- Environmental Concerns: Check periodically the ecological factors, such as temperature variations, moisture levels, and chemical exposures, which can influence the performance of the thermocouple wires. Protective means such as insulation, enclosure, or coating are used to protect the equipment from possible hazards and for the life extension of the equipment.
Troubleshooting Common Issues
Even with the best efforts in installation and maintenance, some problems can still develop in thermocouple wire systems. Therefore, it is essential to ensure that personnel are adequately trained and provided with the following common problem identification and troubleshooting resources for minimal downtimes and maximum system integrity:
- Signal Interference: Look for likely sources of signal interference, like electromagnetic fields, radio frequency interference, and a lack of proper grounding. Shield or reposition sensors to avoid interference with the signal to ensure accuracy in measuring the temperature.
- Sensor drift: Look for signs that the temperature reading becomes progressively inaccurate. Regular calibration checks and re-calibrations are due to correct any drifts and maintain accurate measurements.
- Mechanical Failure: Check all the mechanical parts, such as the connectors, junctions, and protective sheaths, for signs of wearing and damage. Replace worn-out components promptly to preclude the system’s mechanical failure and keep the temperature measurement running.
In A Nutshell
Pelican Wire always lives up to its ideal: leading the way in thermocouple wire manufacturing through tradition and innovation by committing to meet and surpassing industry standards. With knowledge and insight, we move across this vast expanse called temperature measurement. We urge readers to operationalize insights from this comprehensive guide so that they will have the power to take their temperature measurements higher and begin their journey toward precision, reliability, and operational excellence. Reach out to Pelican Wire today.